Tree for the Taking: Tuning Into Sustainability
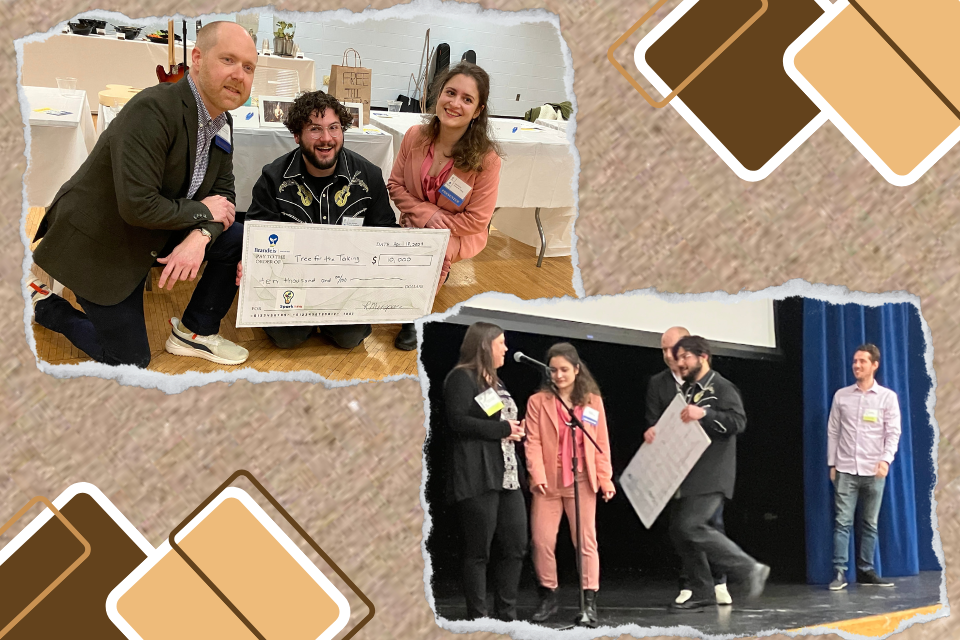
SparkTank first-place winner Tree for the Taking works to craft innovatively sustainable guitars and accessories using waste-wood from invasive trees. Using the invasive species Tree of Heaven, they have worked with the Brandeis MakerLab, as well as participating in the Brandeis Innovation Virtual Incubator, to create a more sustainable, affordable guitar that is good for the planet.
Tree for the Taking is the brainchild of Brandeis Heller School for Social Policy and Management graduates Sam Aronson, ‘20, MBA ‘22, and Alden Kennedy, MBA ‘22. Working together this year as part of the Spark program cohort with PhD candidate Gess Kelley, they developed their business model while creating a prototype. This summer, co-founder Sam Aronson built Tree for the Taking’s first guitar, which is already attracting acclaim from industry experts.
Tree for the Taking seeks to lead the guitar manufacturing industry away from its extractive roots through domestic additive manufacturing, and to further democratize the electric guitar by making them more accessible. It’s an ambitious plan, but one that the team feels confident that they can achieve one step at a time thanks to the skills that they learned at Brandeis. Brandeis Innovation’s Online Infrastructure Manager, Christina Inge, who also teaches the MBA marketing class at Heller, recently spoke with Sam to learn more about the amazing progress that Tree for the Taking has made in the Spark program.
We hear about sustainability as a critical element for many consumers in deciding what to purchase. Tell us about Tree for the Taking and how you envision your sustainable guitar business.
Tree for the Taking is my attempt to transition the guitar manufacturing industry away from its history of deforestation and the globally extractive commodification of exotic timbers. When I think of tools of art creation, of which electric guitars are my favorite, I feel that they should be made in such a way that does not necessitate the cutting of forests all over the world. There has been progress in overall sustainability from many of the major guitar brands over the past decade, but fundamentally almost everything is the same besides that some of the most egregiously deforested woods have been banned. I want to turn otherwise unusable wood from invasive trees into an additively manufacturable composite, alongside exclusively reclaimed or waste wood in order to create a guitar that is as sustainable as it possibly can be.
What is unique about your guitars?
Two things are going to set us apart, the first and most important being that I want to specifically use invasive waste wood to make our guitar without buying any wood that comes from new sources, only otherwise using reclaimed or scrap material. This takes us out of the loop of the fresh timber supply chain, meaning we won’t create new demand for living trees. I’d like to instead be able to traceably remediate the invasive Tree of Heaven, both funding native biodiversity restoration efforts with the sale of the guitars and being able to say where exactly the wood came from. For instance, the prototype I just built has a neck made from salvaged mahogany decking from an actual deck repair I did a few years ago at my Uncle’s house, a slab maple hardwood-flooring fretboard, with a Tree of Heaven composite semi-hollow body, capped with a scrap knotted cedar top that I pulled out of an old warehouse. I collected the Tree of Heaven that I used for the composite from the back of the theater parking lot at Brandeis.
Secondly, rather than taking large billets of material and CNC machining them to subtractively make our guitars, we’re going to be utilizing molds for as many aspects as we can to limit waste and labor-hours in the process. The creation of specialized and custom molds will allow us to cast our parts en masse and then finish them by hand to create a fantastic instrument that not only cuts down on total material waste, but makes the highest and best use of local invasive scrap biomass. Sequestering the waste wood of invasive trees into a durable tool of art creation is vastly superior to burning or composting it, as the carbon will exist in the composite forever rather than enter the atmosphere. The long-term goal is to be able to pop a nearly finished guitar out of a mold without having ever necessitated deforestation locally or abroad. Guitarists should be able to play their guitars with a clear conscience that all of its materials were sustainably and ethically sourced, and could have a deeper connection to a given instrument knowing exactly where the wood came from. Full traceability of origin is present on many bags of coffee today, why not on a guitar?
Tree for the Taking started out when you were a student at Heller. I recall you and your business partner, Alden, working together on a marketing plan for it in my class on marketing, and you mentioned studying your inspiration, Leo Fender, in another class. How did getting your MBA factor into launching your startup?
After several years as a hobbyist woodworker, in 2020 I decided that I loved trees more than just about anything besides guitars. My first inclination was to become an environmental lawyer to set up forest land trusts for guitar manufacturers to help preserve old growth, but only after taking the LSAT did it dawn on me that I would have to learn all of the law just to focus on what I really cared about. So I decided I would get some more business knowledge under my belt so that I could make the difference I wanted to see more entrepreneurially, writing my entire Heller application essay about how morbid it was that we cut down trees to make music with their corpses. At Heller, I was able to better understand not only the environmental harm which exotic timber logging caused, but also the global injustice that this kind of intercontinental extractive industry created throughout history.
When Leo Fender invented the Esquire (later Telecaster) he changed music forever, as its bolt on neck design made guitars cheaper and easier to make and repair. At the onset, he used readily accessible domestic timbers, and created instruments far more durable than the competition. This in my eyes contributed to the birth of rock and roll, by democratizing the guitar and getting it into the hands of more people than ever previously possible. This has happened several times throughout history, with the next largest advancement being the introduction of computer numerical control machining (CNC). I believe that additive manufacturing will be a similarly vast improvement over the coming decades, and I want to be at the forefront of refining its application in luthiery.
You recently made your first guitar under this new brand. It was a detailed process, wasn’t it?
It was actually the first guitar I’ve ever made, period! And I’m over the moon that it not only plays in tune and intonates well, but that I truly love the sound and find it a joy to play. It was a detailed process that required many specialized tools, which made some of the precise operations possible. I am a firm believer that no two things are ever exactly the same, and this is almost never more the case than with instruments. That is why I’m so excited to iterate on my techniques and improve over the next several batches of prototypes, getting to a place where I’m even more proud of the guitars and have learnt what it takes to make a perfect one.
What is some of the feedback you’re hearing from your community about your guitars?
People seem to really like the general aesthetic that I’m going for, with all of the raw materials and woods highlighted with transparent oiled and waxed finishes. We’ve had guitarists reach out and offer to film demos of our “gorgeous” guitar, but I’m waiting until I have a few more built. The soundhole I cut into the top is a to-scale outline of a Tree of Heaven leaf, so that one could theoretically identify this noxious invasive by holding it up to this guitar built using it. One comment was that I could have done something more complicated or ornate with this cut-out leaf shape, even suggesting that I add binding to it, but to me that seemed superfluous. I love the plain leaf, it is as it would be right off the branch.
One thing to be aware of is that neck shapes and profiles are highly personal, and that the first prototype has a very large U-shaped neck to fit my hands on the kinds of chord shapes I typically play. The guitars for production will be more universally dimensioned for the majority of other players, though I would love to be able to offer custom neck profiles to spec, at least while that’s all still done by hand. And finally, obviously the sound is priority one, and people have loved the tones off of the latest demo videos I put out.
You mentioned when we talked that you are inspired by legendary guitar inventor Leo Fender. How has his example guided you?
The most obvious example of his inspiration on me is that I chose to create my first prototype based on his Telecaster, which is really the first production solid body guitar. I wanted to start at square one, because one needs to be able to make a wheel to reinvent it. This was strengthened by the fact that both of my favorite guitarists are Telecaster players, the greatest of all time, Ted Greene and the greatest alive, Julian Lage. I once asked Julian Lage at a masterclass where he would like to see the future of guitar design and manufacturing go, to which he replied that Leo Fender got it right the first time. However, I think that given modern advancements in sustainability of manufacturing methods, there is still work to be done so that good guitars can be built long into the future. With how critical it is that the environment be protected and deforestation stopped, I believe that we can build something while standing on the shoulders of the giants of the past without ruining our planet further. Fenders themselves have had to transition away from some historically used woods in recent years, and I want to diverge from that history at the onset of making our guitars.
What are some of the issues in the guitar making world and the musical instruments industry in general that you’re addressing?
It’s common for guitarists to laud and lust after the most rare and exotic tonewoods of yesteryear, namely Brazilian Rosewood or old-growth spruce. Vintage guitars with Brazilian Rosewood demand huge premiums, with some reaching beyond the quarter-million dollar mark. All I think about when I see those is how many children could attend music lessons for that value, and how much of a loss it is to society when exorbitant capital values are placed on the woods themselves when they caused genuine social and environmental harm. The rainforests of Brazil were decimated by rosewood logging to the point of it being illegal to import, and yet people still build guitars from old reserves of it that then require passports and provenance. Does a guitar with its own passport seem like an accessible tool of art creation? It’d be one thing for an acoustic guitar where its construction materials will have a massive impact on its sound, but for electric guitars where 90% of the sound is just the pickup interacting with the string to create an electrical signal, it is a waste. Taylor made an acoustic guitar out of pallet wood years ago to prove that construction methods could compensate for any kind of material, and I believe the time for electrics to ditch deforestation is long overdue.
So what’s next for Tree for the Taking? How can people support what you’re doing?
Now that I’ve built a guitar out of invasive and reclaimed waste wood, it’s time to hone my luthiery skills and modify the design into something more original and ergonomic. As we prepare to scale, I’ve got to identify the best and most sustainable sources of materials, and invest more into a manufacturing process that ensures the highest possible quality. We’ll be launching a Kickstarter to fund a manufacturing run once we’re set on what our production model will look like. We plan to offer handmade guitar picks and sustainable merchandise in addition to the guitars for those looking to help support our mission. Visit our website at treeforthetaking.com, where we have some of the first picks I ever made still available for purchase.